Reasons And Prevention Of Ion Exchange Resin Particle Breakage
The particles of the ion exchange resins currently used in chemical desalination are complete spheres. During use, a small amount of resin will be broken due to wear, expansion and contraction, which is normal. The accumulation of these broken cation and anion resins in the resin layer will increase the water flow resistance and affect the normal operation of the equipment. Therefore, they should be removed during the backwash of the ion exchanger. Under normal circumstances, the annual loss rate of resin is as follows. When the breakage rate and loss rate of resin particles significantly exceed the normal values, it can be considered that the resin has a breakage problem.
Resin particles may be broken during storage, transportation and use of resins.
Common reasons are:
Poor build quality. During the resin manufacturing process, due to improper maintenance of process parameters, some or a large number of resin particles will be cracked or broken, which is manifested as low crushing strength of resin particles and low sphericity after grinding.
Frozen. Resin particles contain a large amount of moisture. When stored or transported at sub-zero temperatures, this moisture will freeze and expand in volume, causing the resin particles to crack. Frozen resin shows a lot of cracks under the microscope, and serious breakage occurs in a short period of time after use. In order to prevent the resin from being frozen, the resin should be stored at 5 ~ 40 ℃, and avoid transportation during the freezing period.
Dry. When the resin particles are exposed to the air, they will gradually lose their internal moisture, and the resin particles shrink and become smaller. When dry resin is immersed in water, it rapidly absorbs water and expands the particle size, causing cracking and chipping of the resin. For this reason, the resin should be kept sealed to prevent drying out during storage and transportation of the resin. For the resin that has been air-dried, it should be immersed in saturated salt water first, and the high concentration of ions in the solution should be used to suppress the expansion of the resin particles, and then gradually diluted with water to reduce the cracking and breaking of the resin.
The effect of osmotic pressure. Resin under normal operating conditions, during the failure process, the resin particles will generate internal stress of expansion or contraction. In the long-term use of the resin, the repeated expansion and contraction of the resin is the main reason for the crack or breakage of the resin particles. The rate of resin expansion and contraction depends on the rate of resin transformation, which in turn depends on the salt concentration and flow rate of the incoming water.
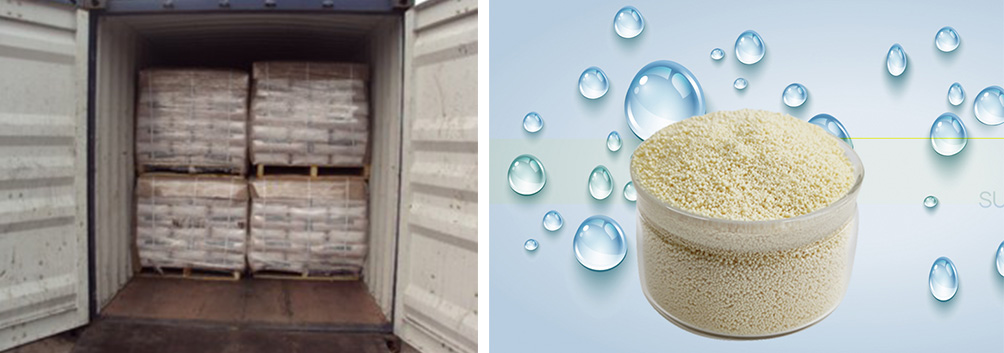
The Annual Loss Rate Of Ion Exchange Resin | |
Resin Name | Annual Loss Rate (%) |
Fixed Bed Resin 001×7 | < 5 |
Fixed Bed Resin 201×7 | < 10 |
Mobile Bed Resin | <10 ~ 15 |
Resin particles may be broken during storage, transportation and use of resins.
Common reasons are:
Poor build quality. During the resin manufacturing process, due to improper maintenance of process parameters, some or a large number of resin particles will be cracked or broken, which is manifested as low crushing strength of resin particles and low sphericity after grinding.
Frozen. Resin particles contain a large amount of moisture. When stored or transported at sub-zero temperatures, this moisture will freeze and expand in volume, causing the resin particles to crack. Frozen resin shows a lot of cracks under the microscope, and serious breakage occurs in a short period of time after use. In order to prevent the resin from being frozen, the resin should be stored at 5 ~ 40 ℃, and avoid transportation during the freezing period.
Dry. When the resin particles are exposed to the air, they will gradually lose their internal moisture, and the resin particles shrink and become smaller. When dry resin is immersed in water, it rapidly absorbs water and expands the particle size, causing cracking and chipping of the resin. For this reason, the resin should be kept sealed to prevent drying out during storage and transportation of the resin. For the resin that has been air-dried, it should be immersed in saturated salt water first, and the high concentration of ions in the solution should be used to suppress the expansion of the resin particles, and then gradually diluted with water to reduce the cracking and breaking of the resin.
The effect of osmotic pressure. Resin under normal operating conditions, during the failure process, the resin particles will generate internal stress of expansion or contraction. In the long-term use of the resin, the repeated expansion and contraction of the resin is the main reason for the crack or breakage of the resin particles. The rate of resin expansion and contraction depends on the rate of resin transformation, which in turn depends on the salt concentration and flow rate of the incoming water.
Last One :
Related Products
-
Wire Cut EDM Resin Mixed Bed Ion Exchange ResinAppearance: Yellow-brown spherical particles.Ionic form:H+/OH-Volume complete exchange capacity(mmol/ml):≥0.6
-
Strong Acid Cation Exchange Resin for water treatmentAppearance: Claybank to tan transparent spherical particle.The degree of crosslinking : 10%.Ionic form:Na+
-
201×7 Anion Exchange ResinAppearance: Light yellow to gold yellow transparency sphericity particles.The degree of crosslinking : 7%.Ionic form:Cl-
Message